Cathodic dip coating and dialysis cells
Cathode dip coating, or CDC for short, is an electrochemical coating process in which components are coated with an electrically conductive, aqueous dip coating in an immersion bath. The paint is deposited by chemical reactions (coagulation) of the binder. The result is a corrosion-resistant, scratch-resistant and acid- and alkali-resistant surface.
Cathodic dip coating is a very environmentally friendly method, as water is used as the solvent. The paint yield is up to 98.5 %, meaning that only 1.5 % of the paint used is discharged. The CDC coating has excellent gripping performance, resulting in a very even coating of metal surfaces and cavities with uniform layer thicknesses and good surface qualities.
CDC coating is used in various areas. In the automotive industry, car bodies, with their complicated workpiece geometry, are given a primer coating as corrosion protection. Due to the good gripping performance, even hard-to-reach areas and cavities of the body are given a thin, homogeneous layer of paint, which makes them corrosion-resistant.
EKK Anlagentechnik offers you a wide range of equipment and accessories for cathodic dip coating. In addition to various types of dialysis cells, we also have accessories for your anolyte system, for busbars and rectifiers as well as for your filter system. Attachments in the basin such as crash rails and flood pipes are also part of our product range.
Take advantage of our many years of experience in the development of efficient production solutions for the automotive industry. You can rely on our expertise. We provide you with competent and reliable advice and work on schedule.
EKK range of services for cathodic dip coating
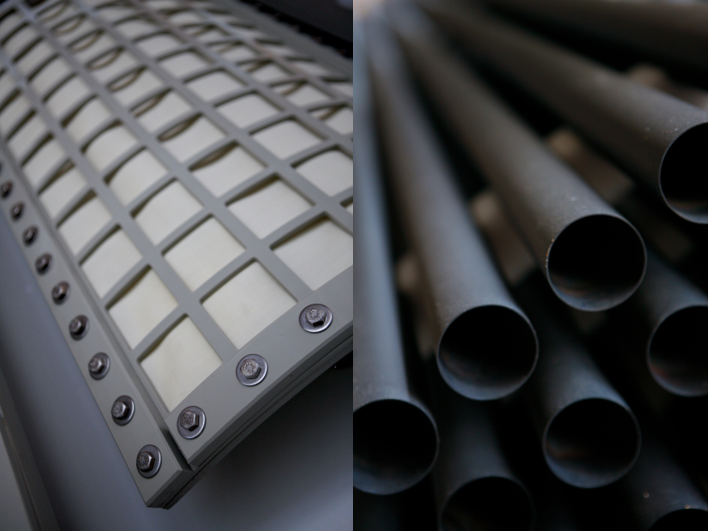
- Consultancy/planning
EKK supports you in selecting the optimum dialysis cell type for your CDC basin. By continuously optimising the manufacturing process in combination with our in-depth consultations, we create the optimum design to suit your basin geometry. - Production
EKK manufactures various types of dialysis cells and has become the world's leading supplier of dialysis cells. - Installation
EKK performs the installation work in the basin and performs the necessary leak tests. - Systems service
EKK carries out the general inspection of your CDC system for you during the annual production pauses and prepares final documentation.
EKK dialysis cells for your CDC basin
Dialysis cells are used as anodes in the CDC basin. They are attached to both sides of the basin wall and form the opposite pole to the body (cathode). Paint depositing takes place in an electroplating process. This is realised by an electrical current flow from the dialysis cell via the conductive paint to the material to be painted.
EKK dialysis cells are equipped with a special anion exchange membrane. During the painting process, interfering anions form in the paint, which are removed from the paint through the membrane into the anolyte. Acid is discharged so that the pH value in the CDC basin remains within the process parameters.
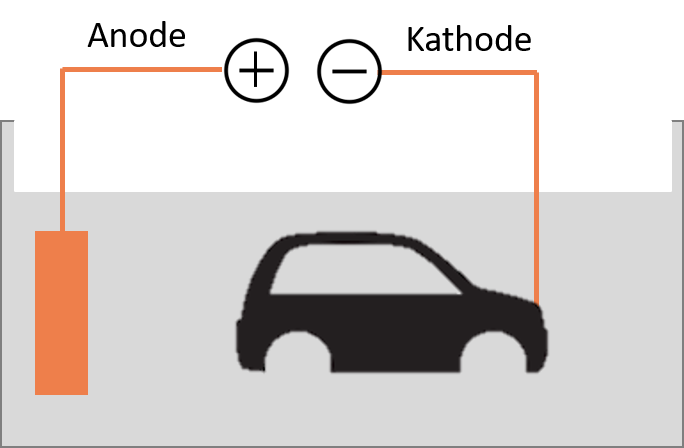
EKK dialysis cell types
The EKK range includes the following types of dialysis cells, which are designed and manufactured according to our customers' requirements. The appropriate type of dialysis cell is selected according to the required anode area and the specified anode/cathode ratio.
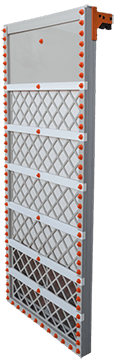
Flat dialysis cells
- Large anode area
- Anode plate (one/two/three-piece)
- Perfect anolyte flow
- Little need for tableau spaces
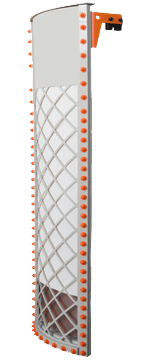
Segment dialysis cells
- Semicircular anode plate
- Perfect anolyte flow
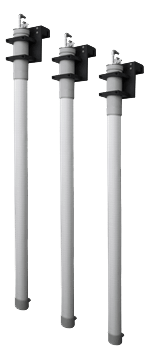
Tubular dialysis cells
- Low weight
- Fast anode control
- Low soiling
- For horizontal and vertical installation
Spare parts and accessories for EKK dialysis cells
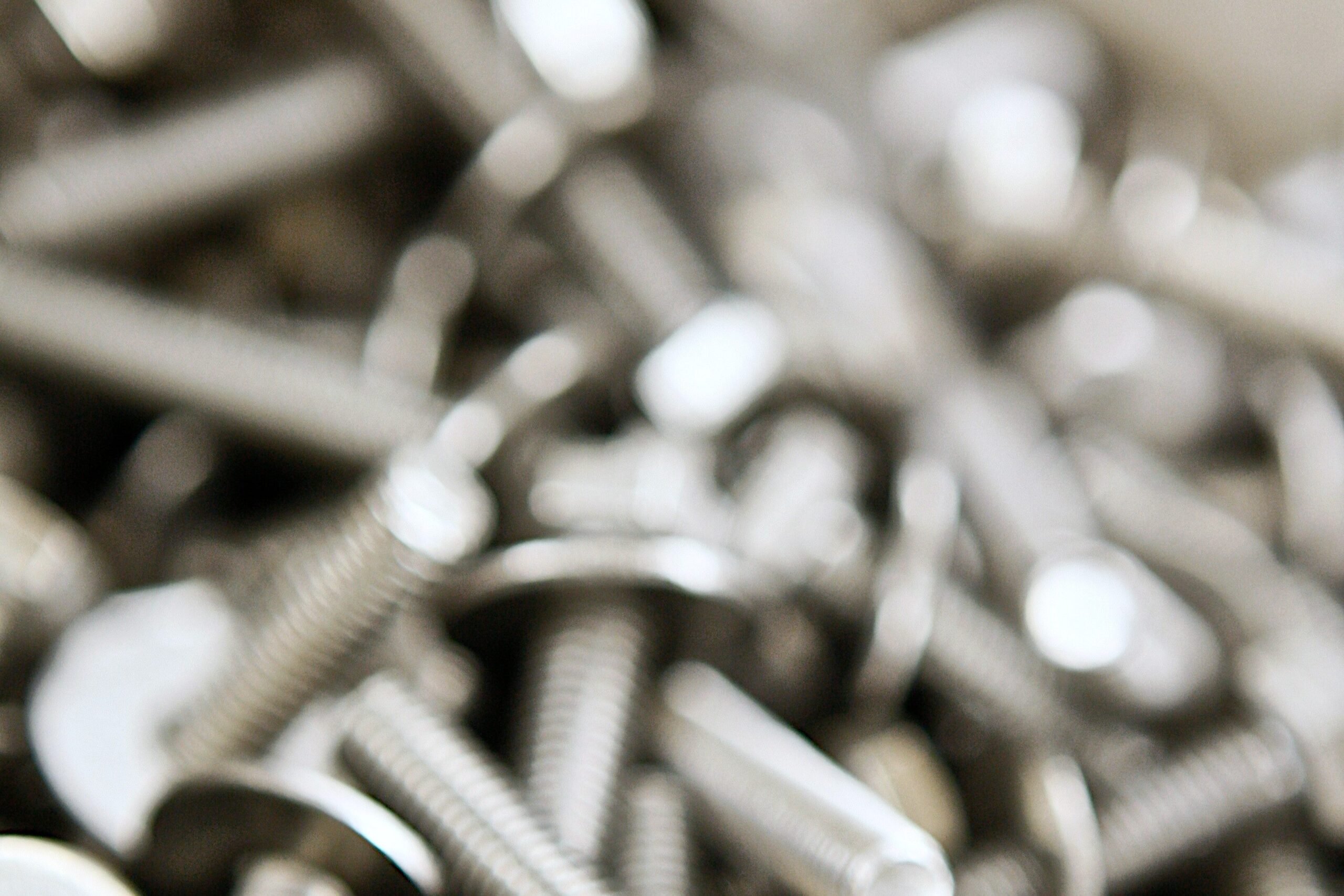
For maintenance and repair work on EKK dialysis cells, we supply the appropriate range of spare parts consisting of
- Membrane envelope
- Anode
- Membrane
- Anode plate
- Spare parts package
and other accessories such as
- Protective cap for submerged tubular dialysis cells
- Mounting system
For easy and safe handling of our segmented or flat dialysis cells, a dialysis cell cross-member is available, which you can also purchase from our shop.
EKK dialysis cell cross-member
The EKK universal cross-member is used for the safe installation and removal of flat or segmented dialysis cells in CDC systems. It is universally applicable and can be used for four different widths.
The EKK dialysis cell cross-member is available with CE labelling. It is designed for a maximum load of 400 kg and is supplied with the appropriate shackles.
For more information on this product, please visit our shop.
Additional anodes
To increase the anode surface area, additional anodes are often used, which can be installed on the basin floor or on the basin wall. For this purpose, there is a choice of free anodes or tubular dialysis cells that are installed horizontally submerged. You will find the appropriate mounting systems required for this in the EKK product portfolio. These are usually customised to the customer's specific installation situation.
Free anodes
- are not connected to the anolyte circuit
- Anode material: Titanium with iridium mixed oxide coating or stainless steel
- Installation on the basin floor
Tubular dialysis cells horizontally submerged
- Equipped with special protective cap
- Anode material: Titanium with iridium mixed oxide coating or stainless steel
- Installation at the edge of the basin (sill tubular dialysis cell) or at the bottom of the basin
Anolyte system
Anolyte is pumped through the dialysis cells in the CDC bath via the anolyte supply lines. Interfering anions form in the paint during the painting process. These are filtered out of the paint by the membrane and disposed of via the anolyte circulation system.
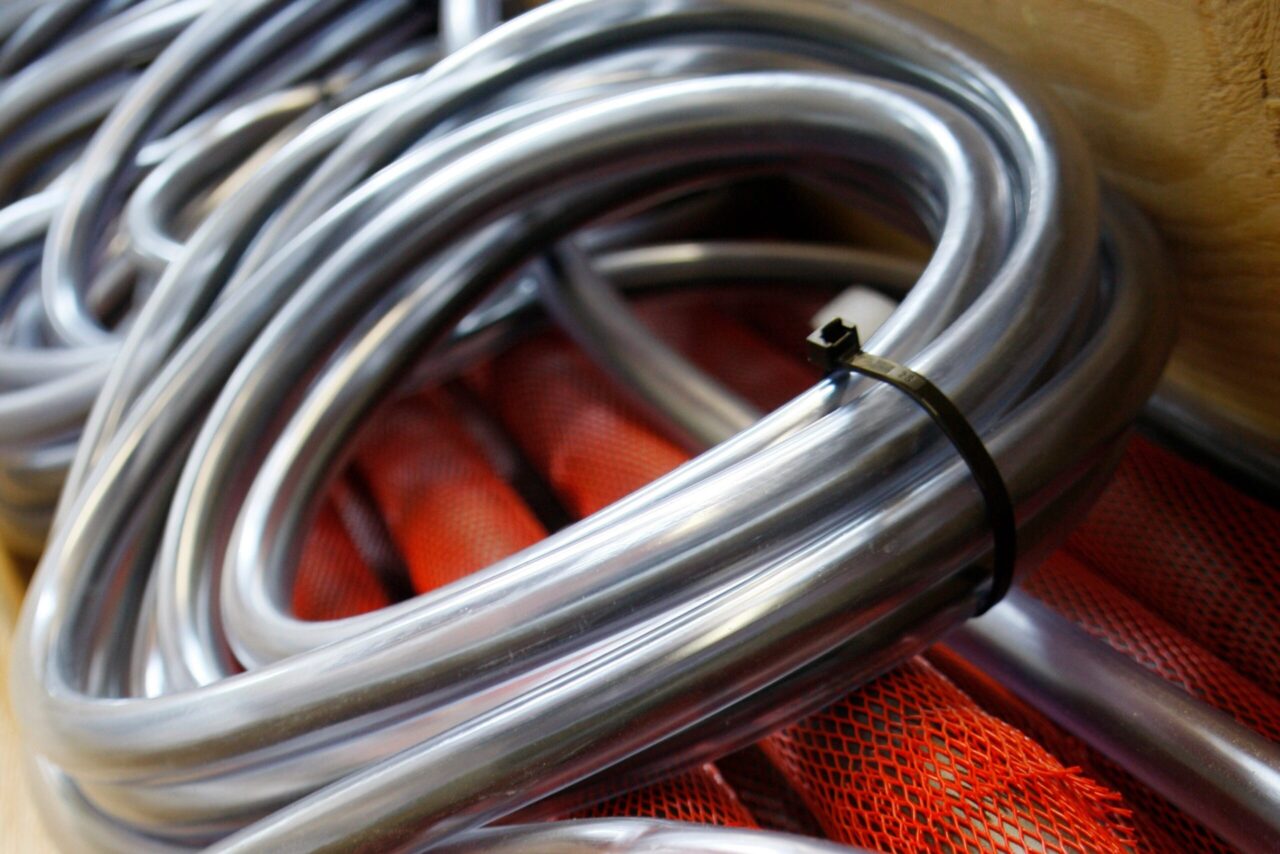
We offer a complete supply package for equipping your anolyte system:
- Anolyte tank
- Anolyte feed pipework
- Anolyte return pipework
- Power cable with power connection
- Tableau
- Pump station
- Filter system
- WES-A sterilisation
Rectifier system
Rectified current is required for CDC coating. Rectifiers supply the system with DC voltage. To avoid excessive current densities, which can lead to coating defects, the voltage applied must be regulated accordingly.

For the power supply, two to three rectifier systems are required for the variable setting of the respective voltage program. Rectifier 1 supplies the immersion area, rectifier 2 the main busbar in the basin and rectifier 3 the outlet area. The current peaks at the start of the deposition are reduced by setting the voltage lower than later in the coating process.
Rectifiers are available in 2 versions:
- Thyristor technology
- IGBT technology
We would be happy to analyse and evaluate your existing system and work with you to develop a concept for optimising and retrofitting your existing system in terms of sustainability and cost-effectiveness.
Busbar
In the CDC system, the busbar forms the cathode connection. Together with the current collectors attached to the conveyor system, it is responsible for power transmission.
We plan your complete busbar and supply the corresponding copper conductor rail elements and connecting rails as well as plastic insulating elements to separate the various rectifier zones.
- Busbar elements
- Connecting elements
- Insulating elements
- Insulating supports
- Mounting systems
- Installation
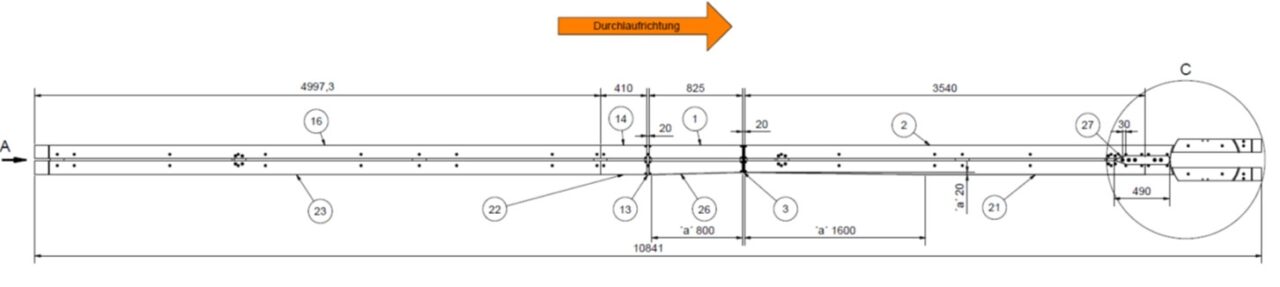
Current collectors
Our scope of delivery includes different types of current collectors, including telescopic current collectors and current collectors with spring clips, which are customised to the needs of our customers and the corresponding installation situation.
Filter technology
Filtration processes are required at various points during the CDC process steps as well as during the multi-stage pre-treatment in order to keep material costs in check and reduce the impact on the environment.
The filter systems are used to remove debris and the ultrafiltration systems to supply the system with rinsing medium (ultrafiltrate) to rinse off paint adhesions, whereby the paint is recovered in a recycling process.
Frequently asked questions about cathodic dip coating:
What are the advantages of the CDC (cathodic dip coating) system technology from EKK Anlagentechnik?
Complex, high-quality, standardised system construction combined with innovation and customer orientation.
Further development based on the existing technology and step-by-step implementation of “Intelligent CDC” future technology.
How sustainable are the products from EKK Anlagentechnik?
Linings with PP-H sheet material are very easy to maintain, as PP is very easy to clean due to its very smooth surface and is also extremely durable.
We offer our customers the service of reprocessing used components such as dialysis cells, thereby contributing to sustainable management in the sense of the circular economy.
What advantages for the CDC process does co-operation with EKK Anlagentechnik offer?
Experience. You benefit from decades of experience and expertise in the overall process and receive sound specialist advice on project management from our competent employees.
Quality. We take all the necessary requirements of the applicable certifications into account during design. When performing orders, all project steps are assured by the installed quality management system.
Everything from a single source. We support you in your projects as a general contractor (GC) or supply you with system components from our own production. We address the relevant technical requirements, such as coating or availability problems, process and production optimisation and increasing the units per cycle. Our process engineering team considers the entire CDC process during project work and also takes the VBH process into account where necessary. The process covers all steps from project planning to operational handover to the customer: in-house planning, design, production and assembly at the customer's premises.
Short response time. Due to the flat hierarchies in our company, we guarantee short response times. For you, this means short delivery times for components and spare parts as well as short-term on-site deployment, which increases your production and process reliability.
Which materials can be coated with CDC?
In principle, metallic components and metal surfaces can be coated using CDC technology.
How long does the CDC process take?
The process time for CDC coating depends on the amperage and the desired coating thickness and is approx. 2 – 8 minutes.
What pre-treatments are necessary before CDC?
The components to be coated must undergo pre-treatment for CDC coating. In addition to the typical degreasing and pickling, this also includes the process steps of activating, phosphating and passivating. After CDC coating, the applied paint layer is cross-linked in a drying oven, making it hard and durable.
How thick is the coating after cathodic dip coating?
With cathodic dip coating, layer thicknesses of up to 60 μm can be produced.
Where is CDC typically used?
CDC coating is used in various industrial sectors, e.g., automotive and general vehicle construction, electrical industry, agricultural machinery and lorry industry and many more. In addition to vehicle bodies, switch cabinets, radiators, engine housings, steel frames, window and door fittings and sheet metal panelling are also coated.
Is cathodic dip coating environmentally friendly?
Cathodic dip coating is a very environmentally friendly coating method, as the paint is water-based and therefore largely solvent-free. The paint yield is up to 98.5 %, meaning that only 1.5 % of the paint used is discharged.